Khana and Ilkal ecosystem
The foundation to understanding any craft involves understanding the people , process and place that support the existence of the craft. Every visit to the cluster there was a new insight into the system within which the craft exists. To make one fabric there are so many sets of people and communities involved. Each of them comes with deep knowledge and skill associated with various stages of making. Below is a small peek into the world of Khana and Ilkal from the three years of engaging with the craft.
The town of Guledgudda in Bagalkot district is known for the Khana textile. The town once bustled with handloom weavers , every house had 4 to 6 looms and the women of the household would be involved in ancillary weaving activities like bobbin winding, pirn winding and warp joining while the men sat on the pit looms to weave.
One craft could provide livelihood for the entire town. Pre-loom processes like reed making, lattice making, bobbin winding, warp joining, warp cleaning, drafting and loom setting provided employment to a variety of communities in the town. The surrounding villages like Sulebhavi, Amingad, Kerur, Kamatigi would depend on silk to supplied from guledgudda while some loom parts and equipment would be available in these towns.
Weaving communities like the Devanga, padmashali, pattashali, and kuruvinshettys are involved in the various processes associated with weaving these Khana and Ilkal textiles.

Listed below are the skills and processes involved in weaving the Khana and Ilkal textiles. It involves the expertise of many varied artisans. The biggest challenge the craft faces today is the disintegrating ecosystem of artisans who make this possible.
Warping
Twisting
Reeling
Silk rearing
Degumming
Dyeing
Bobbin Winding
Hand Warping
Warp Cleaning
Warp Joining
Interlooping warp of the Body with the Pallu (Ilkal)
Reed making with jowar stem
Drafting reed
Lattice making / pegging
Dobby setting
Loom setting
Pirn Winding


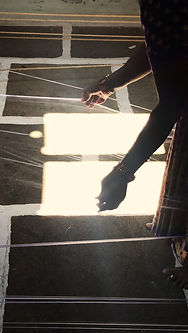
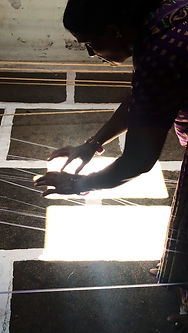
It is believed that not anybody can handle silk, it requires the touch of weavers hand that has softened overtime and grown accustomed to handling the many minute ends of this fiber.

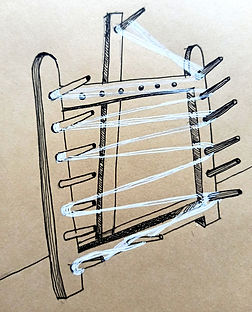

Drafting of the reed involves extremely skilled artisans who thread the reed based on traditional patterns followed in the cluster in accordance with the number of shafts and motif involved in the design. Each motif is unique and requires its own set up before the reed is set up on loom

Warping - an essential hand skill traditionally practiced by the women of the household. A wooden peg warp is used in this cluster and lengths adjusted to the exact 6 yard mark.

Reed making - a highly skilled part of the process that involved selection , cutting and tying of the jowar stem at specific distances based on the composition of the fabric being woven. Each toothpick like jowar stem is individually tied at the perfect distance
Lattice pegging and making that involves drafting a graph and attaching pegs on the lattice to create the traditional Khana motifs

Women artisans who are play a pivotal role in the craft are involved in joining the base warp and extra warp on loom - end by end with natural resin before starting the process of weaving

A couple of thousand ends are drawn through the heild wires which are then connected to the shafts that connect to the barrel dobby levers that lift in a specific pattern based on the motif being woven
Weavers have the expertise of coordinated body movements that involve pedaling to lift the threads forming seamless motifs across the surface of the textile.
Inter-looping of the warp yarns of body and pallu end by end - a technique specific to the ilkal saree weaving.

Women artisans who are play a pivotal role in the craft are involved in joining the base warp and extra warp on loom - end by end with natural resin before starting the process of weaving
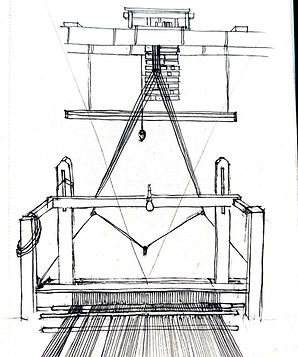